A study at Harvard found that over 40% of shoppers go to another store when a product is out of stock instead of looking for a substitution. This is how customers behave today. Call it impatience or savviness, but stockouts are every business鈥檚 problem.
And they鈥檙e a big, expensive problem.
It鈥檚 estimated that they cause retailers almost one trillion dollars in lost sales worldwide. One reason for this is the ubiquity of online shopping (lookin鈥 at you, Amazon). Most modern consumers don鈥檛 wait for inventory to be replenished. They head somewhere else.
But predicting erratic supply and demand is tough. No one has any idea what鈥檚 coming next. In 1950, a guy invented something called the Magic 8-Ball, but it didn鈥檛 work. Nothing worked.
That is, until modern inventory forecasting. Today鈥檚 manufacturers, suppliers, and retailers rely on software to smooth the edges of uncertainty. Safety stock, buffer inventory, and anticipation inventory are all ways they do it (see what is inventory). This is true in both B2B vs. B2C businesses.
Will reading this post help you make informed decisions about the risks and rewards associated with holding extra stock? According to our Magic 8-Ball, signs point to yes.
What Is Safety Stock Inventory? Safety Stock Definition
Safety stock inventory is extra product kept on hand to account for unexpected delays from suppliers. Safety stock is always held in warehousing when there is uncertainty in supply. It's an effective insurance policy against stockouts, AKA running out of raw materials inventory, finished goods inventory, or packaging.
The Purpose of Safety Stock Is to ...
The purpose of safety stock is to have enough inventory to account for unanticipated shortages. It鈥檚 to prevent the loss of finished goods inventory and sales-ready customers. Gotta keep that work in process inventory pumping away and your order management specialist busy.
These customers are so sales-ready, they鈥檙e literally trying to give you their money. Failing to convert them is inexcusable lost revenue and a poor reflection on your business. But it鈥檚 a problem easily fixed with the right safety stock levels. This is important even for businesses who participate in a consignment inventory model or other non-traditional partnerships.
The Importance of Safety Stock In the Inventory Management Process
Not only do stockouts represent direct sales loss, they erode brand reputation and customer loyalty. Doesn鈥檛 matter if you鈥檙e a retailer losing public trust or a wholesaler that can鈥檛 deliver (see how to buy wholesale). When your customers can鈥檛 get what they want, they remember it. It also affects you inventory carrying cost, so it's important to control.
Is Cycle Stock Safety Stock a Thing?
There is some confusion around cycle inventory vs. safety stock, but it鈥檚 easily clarified. Cycle stock and safety stock are defined against each other.
Cycle stock is the amount of inventory a business cycles through to satisfy regular inventory supply or demand. Safety stock, on the other hand, is the amount of inventory needed to avoid stockouts in the event of unanticipated supply.
That means cycle stock inventory is the amount of inventory on-hand minus safety and buffer stock.
Wait, buffer stock?
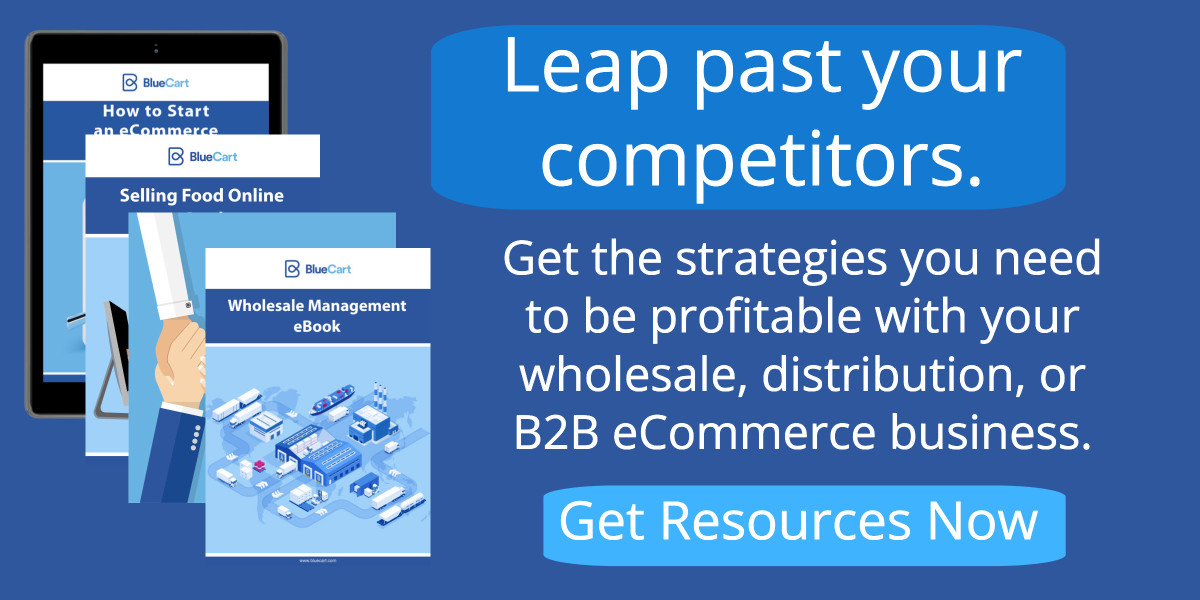
Buffer Inventory Meaning: Define Buffer Inventory
Buffer stock is the amount required to hedge against customer-induced variations, or spikes in demand. It鈥檚 similar to safety stock. Sometimes it鈥檚 even called 鈥渂uffer safety inventory.鈥
But safety stock is the amount required to hedge against supply-induced variations, or shortages in supply. Buffer inventory is required as insurance to protect customers from stockouts of finished product inventory. Make sure you calculate your lead time (what is lead time?) and fill rate correctly so you avoid having too little stock on-hand.
Example of Buffer Inventory
Here鈥檚 an illustrative buffer inventory example. Consider a manufacturer and wholesaler of jams and jellies.
They keep extra levels of raw materials like fruit and sugar on hand to account for disruptions from their supplier. This is their safety stock. It ensures they鈥檙e able to keep production running in the event of an unexpected raw material shortage.
They also keep on-hand extra inventory of jam sealed in jars, labeled, and ready for sale. This is their buffer stock. It ensures they鈥檙e able to keep converting sales in the event of an unexpected demand spike.
Vendor managed inventory agreements and smart pipeline inventory management can help stem a lot of miscalculation. But not every fluctuation in supply and demand is unanticipated.
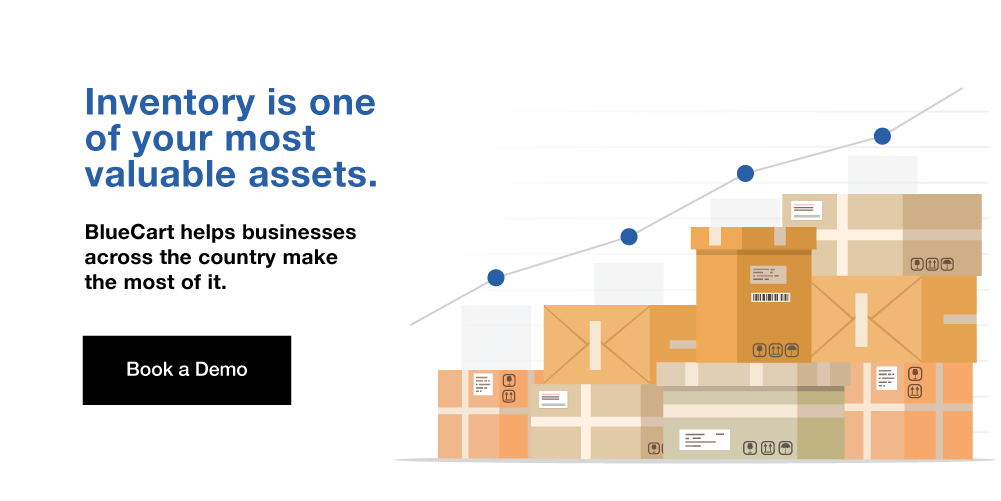
鈥
What Is Anticipation Inventory?
Anticipation inventory is yet another speculative inventory strategy. As can be reasonably inferred from its name, anticipation isn鈥檛 in the business of protecting against unforeseen shortages or demand. It鈥檚 about taking advantage of historical trends.
Anticipation Inventory Definition
Anticipation inventory is goods kept on-hand to account for expected spikes in demand. These foreseen spikes in demand can be because of seasonality, holidays, current events, or trends. Another name for anticipation inventory is smoothing inventory.
Accurate forecasting of anticipated demand isn鈥檛 easy. That鈥檚 why inventory management software is used for all types of inventory, manufacturing inventory, demand planning software, and 惭搁翱听颈苍惫别苍迟辞谤测 included.
Anticipation Inventory vs Safety Stock
Anticipation inventory is like safety stock. But instead of hedging against uncertainty, it represents a prediction of demand increase. You expect the sell through rate of anticipation inventory to be quicker than safety stock because they will be around for fewer inventory days.
A good example is a clothing company knowing that outerwear purchases as winter approaches. They鈥檒l work to acquire enough coats, scarves, hats, and the rest of it in anticipation of the spike in demand.
Quiz: The Primary Lever to Reduce Anticipation Inventory Is to
Here鈥檚 an anticipation inventory quiz for you. If you get the following question right, you'll have a much better grasp on the ways to perform inventory reduction.
The primary lever to reduce anticipation inventory is to:
- Improve inventory forecasting so there are less surprises
- Produce or acquire inventory in line with demand levels
- Increase safety stock and buffer inventory
- Get more equipment and more employees
The correct answer is B. The only way to reduce anticipation inventory is to get production closer to demand levels.
Extra Stock: A Balancing Act
Safety stock, buffer inventory, and anticipation stock sound well and good. But there is a cost to holding inventory鈥攏o matter the reason why.
- You pay for the space to store that inventory.
- That space can no longer be used for items with a higher inventory turnover rate.
- You need more staff and security to handle and protect more inventory.
- You risk extra stock becoming obsolete.
- Storage costs can cut into your ability to hit your inventory KPI.
The accepted total cost of holding inventory is roughly 20 to 40% of the cost of your merchandise inventory. That leaves every company with an important calculation. What鈥檚 higher, loss from stock outs or loss from holding inventory?
The answer to that question depends on your business. Supply and demand are in an eternal push-and-pull with risk and cost. Business owners will forever straddle that line. Inventory management is the science of dealing with uncertainty, and the variables it considers can never be completely controlled. Keeping stock levels at the optimal levels is valuable and worth paying a high warehouse manager salary for.
Consistent decision making based on a deep understanding of risk level and cost is what success looks like. You also need to conduct a regular inventory audit to avoid safety stock becoming dead stock (see dead stock meaning).
Thankfully, modern online marketplace and inventory management software makes that easier for businesses. So if you鈥檙e looking to sharpen up your safety and buffer game, you鈥檇 do well to find an automated platform with robust forecasting. Using a B2B ecommerce platform can also help you acquire more B2B sales leads (see what is B2B sales) and sell more product quickly.
Frequently Asked Questions About Safety Stock
Safety stock prevents you from running out of product when your supplier is delayed or you鈥檙e experiencing higher-than-normal demand. In order to keep costs low, it鈥檚 good to know how much safety stock you should have on hand. Read our answers to commonly asked questions below:聽
How do you calculate safety stock?
The appropriate amount of safety stock to keep on hand can be calculated with this formula:
- Step 1: Average daily sales of product x average lead time = average safety stock
- Step 2: Maximum daily sales of product x maximum lead time = maximum safety stock
- Step 3: Step 2 result - Step 1 result = optimal safety stock
Having an optimal amount of safety stock ensures you can address demand surges without inventory holding costs being too high. Make sure to periodically update your safety stock based on fluctuations in demand and supplier timelines.聽
What is buffer in supply chain?
Supply chain buffer is another term for safety stock. Buffer stock is an increase in the amount of stock you order to account for shipping delays, spoilage, and customer demand variability.聽
Buffer should be used wisely. It鈥檚 not a replacement for regular inventory; it鈥檚 simply a backup. It gives you peace of mind and operational flexibility when production halts, accidents happen, or customers buy more out of nowhere.
What is a good safety stock level?
A good safety stock level is the difference between a product鈥檚 maximum daily sales and its average daily sales, times the product鈥檚 average lead time.
This provides enough spare units of a product to sell in the event of rapid demand fluctuation. Even the fastest lead times are usually two weeks, and you can鈥檛 rely on that when you need products to sell right now.
How to Forcast Sales and Safety Stock Needs?
The right amount of buffer stock should be decided based on sales forecasts. In order to forecast sales, businesses need to gather data from all sales channels. The data should be then combined and summarized. Only then can it be analyzed in order to determine the right buffer inventory level. Small businesses can afford to have higher buffer stock levels but large enterprises will have very high storage costs if they don鈥檛 have optimal safety stock levels.
What Is the Formula for Safety Stock?
(袦aximum daily sales X maximum lead time) 鈥 (average daily sales X average lead time) = Safety stock. That is the basic formula for buffer stock. However, it might differ based on factors like seasonality, planned marketing campaigns, or other factors that might increase or decrease sales.
Let鈥檚 examine the main components of the formula:
- Maximum daily sales 鈥 it can be tracked with the help of a sales tracking system or another software with this functionality;聽
- Average daily sales 鈥 the average daily sales is the sum of all sales for a specific period divided by the number of days;
- Maximum lead time 鈥 this metric shows the maximum number of days it took for a stock shipment to arrive after it鈥檚 been ordered;
- Average lead time 鈥 similar to the average daily sales, this metric is the sum of all the days between the order and its delivery divided by the number of shipments. For example, if you restocked 4 times during a period of time and two of those times the stock arrived on the fifth day while the other two times it took 7 days. When we calculate 5+5+7+7, we get 24. When we divide that by 4 (number of shipments), the average lead time is 6 days.